Technological Challenge
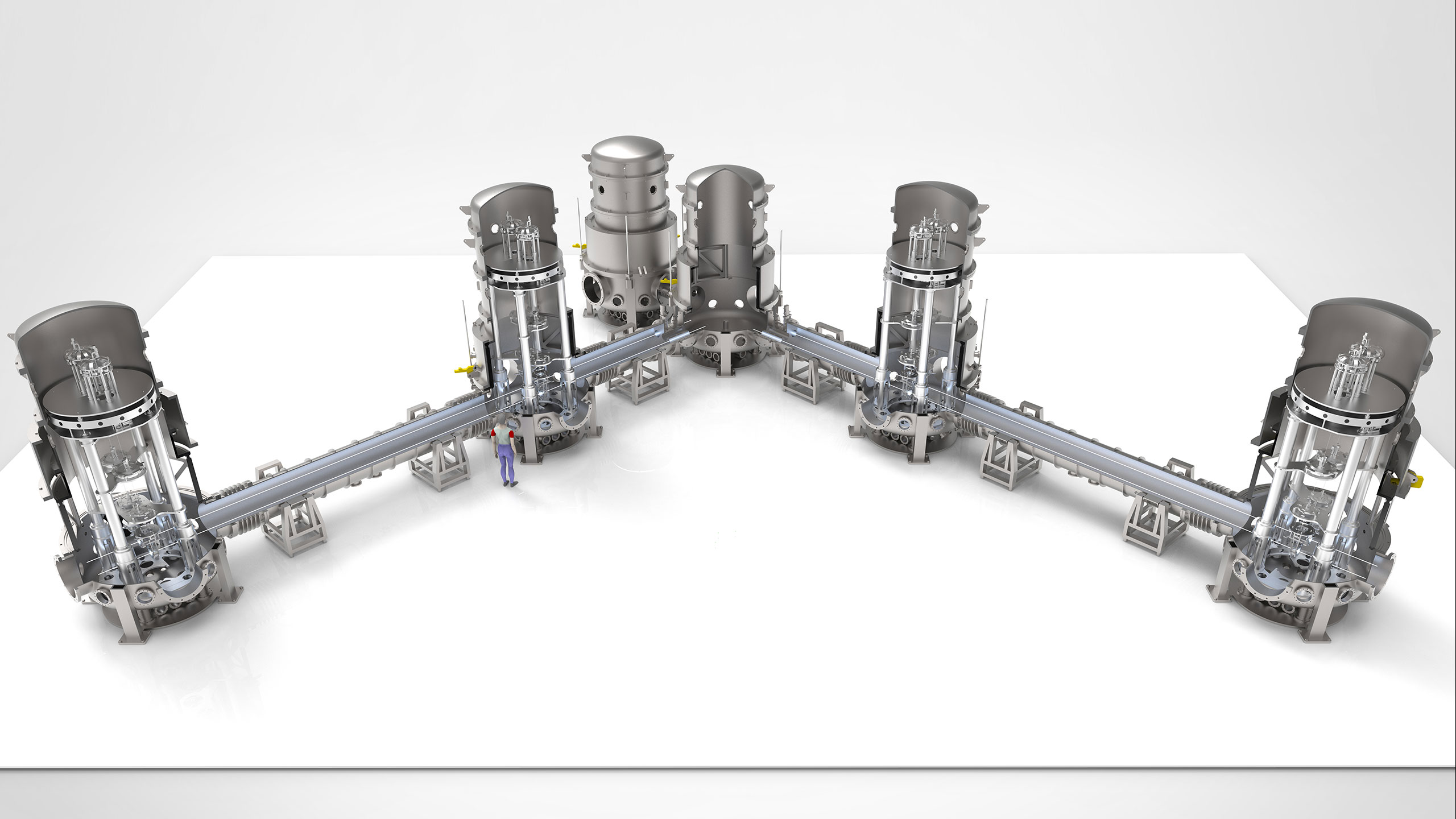
The future Einstein Telescope (ET) is a gravitational-wave observatory that relies on the measurement of minute relative length differences between the kilometer-scale long arms of a laser interferometer. Optical systems are a crucial aspect of ET: the few 100 kg heavy, super-polished mirrors with highly optimized coatings at the ends of the arms serve as test masses; an ultra-stable laser provides the monochromatic laser beams that probe the test masses; numerous additional optical systems and sensors serve to control and stabilize the instrument to be able to detect the signature of the passage of a gravitational wave through ET as a minute ‘flicker’ in the photodetector (photodiode) output registering the intensity of the recombined laser beams.
The astonishing precision, 10–18 m relative mirror displacements, demonstrated by the LIGO and Virgo observatories in their Nobel-Prize winning first detections of gravitational waves (2015-2019) rely on an optimal combination and tuning of the world’s best lasers and optical equipment. To build up the several hundreds of kW laser power in the arms (optical resonators) of the interferometer, round-trip losses must be less than 50 ppm. Similarly, wave-front distortions and scattering of the light field into higher-order spatial modes must be kept to a minimum and the laser must have extremely low amplitude and phase noise, as well as a very stable pointing accuracy.
Mirrors:
Both the LIGO and Virgo observatories use ultra-pure fused silica for their mirrors. To reduce the influence of thermal noise of the mirror surface, especially from coatings, large laser beams with around 10 cm diameter are employed. Correspondingly, the mirrors need a diameter of around 50 cm such that the diffraction loss is negligible. These mirrors (around 40 kg each) are polished with a radius of curvature of about 2 km, with flatness of ±2 nm and a root-mean-square roughness of less than 0.1 nm. This precision is achieved using electro-polishing, ion-beam figuring and corrective (multi-layer) coatings. The reflectivity of these mirrors is 99,999% and the measured bulk absorption per centimeter is below 1 ppm. These mirrors are suspended from four fused-silica fibers with a few hundred µm diameter.
Lasers:
All current gravitational-wave detectors operate at a continuous-wave laser wavelength of 1064nm, making use of the highly stable solid-state (NPRO) Nd:YAG design as a seed source. The laser is further amplified to around 100W and spatially filtered to possess a very clean fundamental Gaussian profile. A hierarchy of high-bandwidth control loops and pre-stabilization steps link the laser frequency to the kilometer-long resonators of the interferometer, ultimately achieving a frequency stability of 1µHz/Hz-1/2.
Relation to the Einstein Telescope
Innovation
- One of the unique features of the Einstein Telescope is to use cryogenically cooled mirrors to significantly improve the detection rate for low gravitational-wave frequencies (below 20 Hz) by reducing the thermal noise in notably the mirror coatings and suspensions. Crystalline silicon, a well-known material from semiconductor industries, is ideal for this purpose: apart from its excellent mechanical quality factor, silicon exhibits a negligible coefficient of thermal expansion at temperatures around 120 and below 20 K and even more importantly it becomes an excellent thermal conductor at low temperature. Thermal mirror deformations will be strongly reduced compared to fused-silica mirrors.
- Switching from fused silica to crystalline silicon requires a different laser light wavelength for the bulk mirror material to be transparent. This can be achieved at wavelengths of 1550nm and above, with around 2µm favored from optical-coating considerations. New lasers, respecting the stringent constraints on power stability, pointing, etc., and many new sensors need to be developed. In particular, low-noise, high-efficiency large-area sensors for beam monitoring and wavefront sensing will be required.
- Regarding the crystalline silicon substrate or ingot, the bulk absorption of the laser light heating up the mirrors must be kept below about 5 ppm/cm to be able to maintain, notably for 20 K operations, the mirrors at a stable cryogenic temperature. Since residual free charge carriers dominate absorption at the envisaged 1.5 – 2.0 µm wavelengths, high resistivity substrates (better than 10 kΩ cm) are required. Whereas float-zone grown silicon achieves the required high resistivity, it is technically limited to smaller diameters. Growth processes that achieve large substrate sizes with low impurities, for example magnetically assisted Czochralsky processes, need to be further explored.
- The polishing specifications of the silicon will be similar to the very demanding requirements that were achieved with fused silica for the LIGO and Virgo observatories. Polishing processes that can deliver the same specifications on silicon substrates will have to be investigated and their quality proven through suitable metrology, including parameters such as transmitted wavefront distortion and absorption. In view of the different wavelength and in view of the cryogenic temperature operations, entirely new multi-layer coatings have to be developed. This is probably one of the most challenging issues regarding the mirrors and a hot area of research in the world-wide gravitational-waves research community.
- Finally, in the last stage of the vibration attenuators, the mirrors are envisaged to be suspended from few mm diameter crystalline silicon ‘rods’. With crystalline silicon rods at cryogenic temperatures an excellent thermal conductivity will be achieved and using the same material for the rods and the mirrors minimizes mechanical loss. A major challenge will be to procure such rods with lengths of 1-2 meters and with excellent mechanical quality (scratch-free surfaces) to be able to carry the mirror load of 100-200 kg reliably, i.e., without the risk of ruptures.
Industrial relevance and further application fields
A list of all certain and potential mirrors needed for gravitational-waves and other experiments and detectors has been composed and is openly available. This list contains mirrors of several sizes, materials, and qualities. Next to a high number of smaller mirrors, a total of about 140 super high-quality silicon mirrors with masses between about 100 and 300 kg will be needed over the coming years and in particular from around 2030 onwards many will be needed for the Einstein Telescope. Notably the large mirrors will require new procedures to procure, validate and test them. We are looking for companies that are willing to invest in developing such mirrors. There is a high possibility that the first company (or companies) to reach the design specifications will be the one(s) to receive large orders. Given the overlap between our specifications (mirror surface characteristics) and important noise sources (thermal mirror deformations) and those in the nanolithography industry we foresee interest in that sector as well.
References
For further information and more details about this technology field, please check the following Einstein Telescope Design Reports.
E-TEST Conceptual Design Report:
Einstein Telescope Conceptual Design Report:
Optics: Pages 93-101 & 122-123
Contact to the Einstein Telescope ecosystem
Are you active in this field of technology? Do you have an innovative approach to meet the requirements for optics? Then take note of our tenders, join our challenges or simply get in contact with us. Furthermore, you can take a look at the mapping displaying the ET-relevant cempetencies in the EMR-Region. If you would like to be part of this mapping, please contact the business development managers.
Business development contacts
Peter Gier
AGIT DE – p.gier@agit.de
Matthias Grosch
NMWP.NRW DE – matthias.grosch@nmwp.de
Michel Stassart
Skywin BE – michel.stassart@skywin.be
Annick Pierrard
ULiège BE – a.pierrard@uliege.be
Maxime Corvilain
POM Limburg BE – maxime.corvilain@pomlimburg.be
René Kessen
LIOF NL – rene.kessen@liof.nl
Scientific contacts
Sebastian Steinlechner
Maastricht University (NL) – s.steinlechner@maastrichtuniversity.nl