Technological Challenge
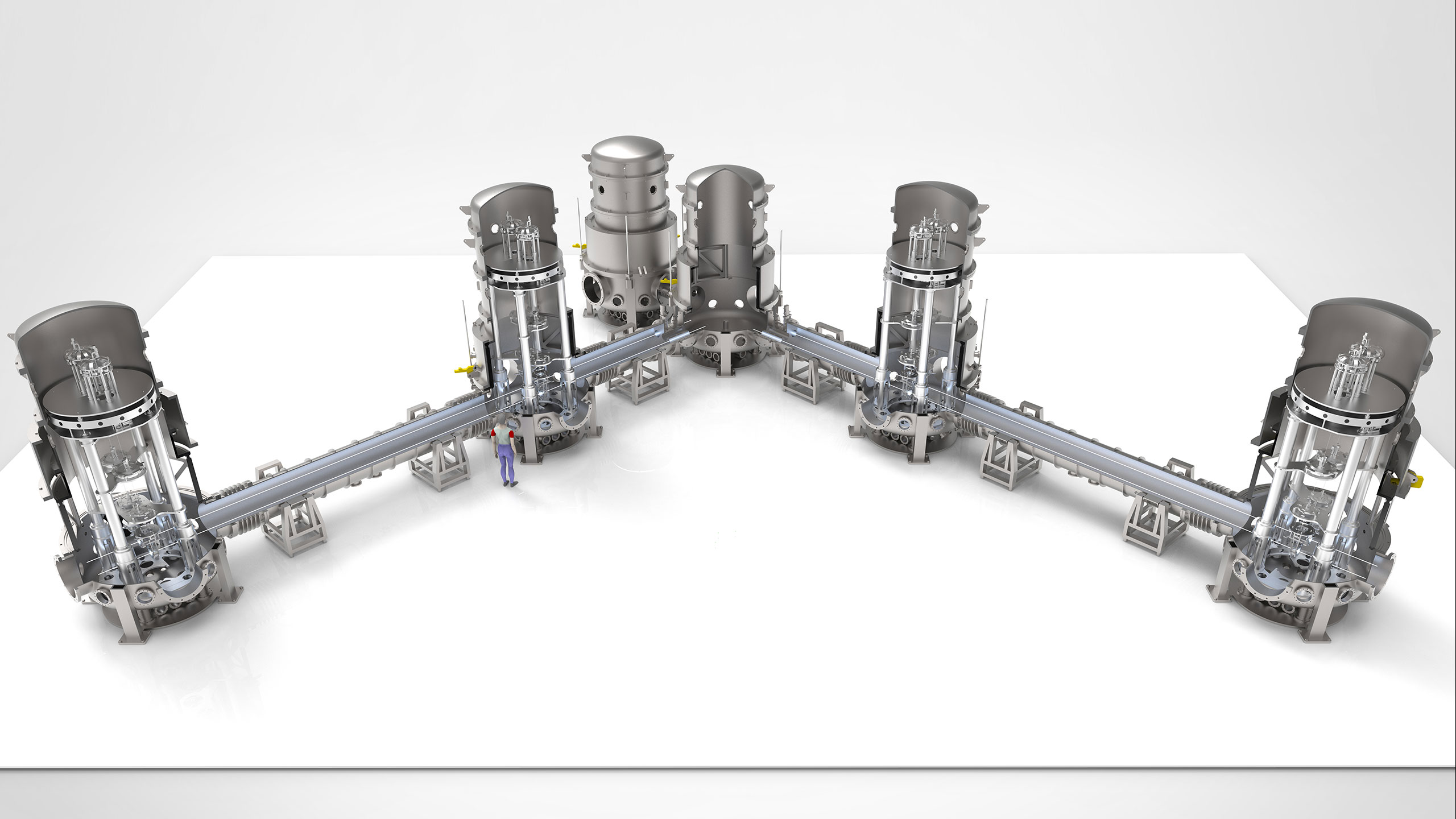
Vibration isolation systems have the function to isolate equipment from all source of disturbances and in particular from seismic motion. Typically, two different types of vibration needs to be reduced:
- Horizontal vibrations (via a chain of pendulums)
- Vertical vibrations (via elastic elements of maragin steels, bodies of inertia)
For this, characteristically slow mechanical systems are required with a period of 5-10 s. The systems traditionally consist of blades, springs, wires and stiff combinations (i.e. thin metal).
These components can be long (1-5 m) and are composed of different materials such as stainless maragin steel, aluminum alloys with different characteristics (e.g. stiffness) depending on their location.
Relation to the Einstein Telescope
Relation to the Einstein Telescope
In order to reach the observation sensitivity, most of the instrument has to be made of ultra-precise components, drastically isolated from all source of disturbances, and in particular from seismic motion.
As an example, about 200 in-vacuum vibration isolation systems are needed for core and recycling optics, input mode cleaners, optical benches, mirrors of filter cavities…which means:
- >5000 blade springs
- >1000 suspension wires
- >1000 inertial sensors
- >5000 displacement sensors
- >5000 actuators
For Einstein telescope, three vibration isolation systems are required for room temperature (i.e. high frequency). In addition, three systems are required in cryogenic conditions.
Innovation
- Components need to be able to cope with ultra-high vacuum conditions
- Need for very clean components (no impurities), welding cleanings need to be very strict for these ultra-high vacuum components. Potential contaminants are dust (which eats the suspension fiber components). In additions, the presence of hydrocarbon should be avoided at all cost. In the stringent conditions, these become very volatile and can stick to the mirror, resulting in black spots.
- for the systems functioning in cryogenic systems, it is crucial that the detectors have no contact (do not touch) and more crystalline materials will be suitable for the mirror.
- For the actuators, coils are required for non-contacting systems in cryogenic systems. Design is not made yet.
- For the displacement sensors, custom-made specifications are required for functioning in cryogenic conditions.
- Spring elements are difficult to obtain, since the required material (maragin steel) is very special type of maragin steel, mostly used in aerospace.
Industrial relevance and further application fields
These components can enter other markets for instance in, where the requirements for these mechanical parts are very stringent as well:
- Aerospace
- Automotive
- Space travel
References
For further information and more details about this technology field, please check the following Einstein Telescope Design Reports.
E-TEST Conceptual Design Report:
Einstein Telescope Conceptual Design Report:
Contact to the Einstein Telescope ecosystem
Are you active in this field of technology? Do you have an innovative approach to meet the requirements for precision mechanics and mechatronics? Then take note of our tenders, join our challenges or simply get in contact with us. Furthermore, you can take a look at the mapping displaying the ET-relevant cempetencies in the EMR-Region. If you would like to be part of this mappink, please contact the business development managers.
Business development contacts
Peter Gier
AGIT DE – p.gier@agit.de
Matthias Grosch
NMWP.NRW DE – matthias.grosch@nmwp.de
Michel Stassart
Skywin BE – michel.stassart@skywin.be
Annick Pierrard
ULiège BE – a.pierrard@uliege.be
Maxime Corvilain
POM Limburg BE – maxime.corvilain@pomlimburg.be
René Kessen
LIOF NL – rene.kessen@liof.nl
Scientific contacts
Prof. Christophe Collette
PML – A&M – ULiège BE – christophe.collette@uliege.be
Dr. Alessandro Bertolini
Nikhef NL – alberto@nikhef.nl